FMEA
Failure Mode and Effect Analysis
Fehler Möglichkeits –und –Einfluß –Analyse
Die Basis einer effektiven FMEA ist die Interaktion zwischen den einzelnen Schritten:
Materialflussdiagramm ⇨ FMEA ⇨ Produktionslenkungsplan ⇨ Arbeitsanweisungen (AA) ⇨ Aufzeichnungen
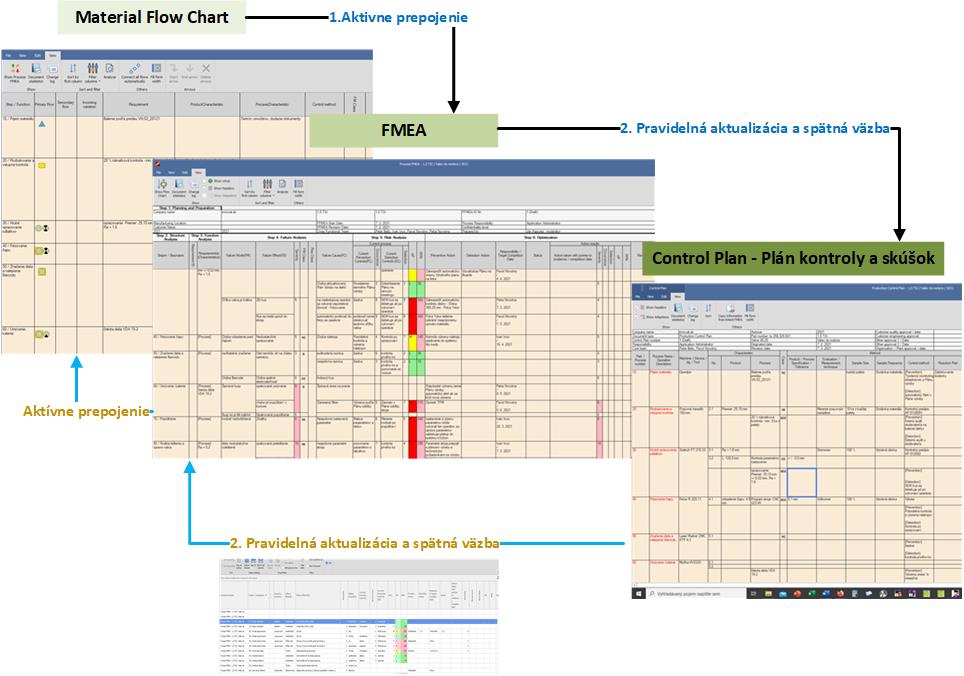
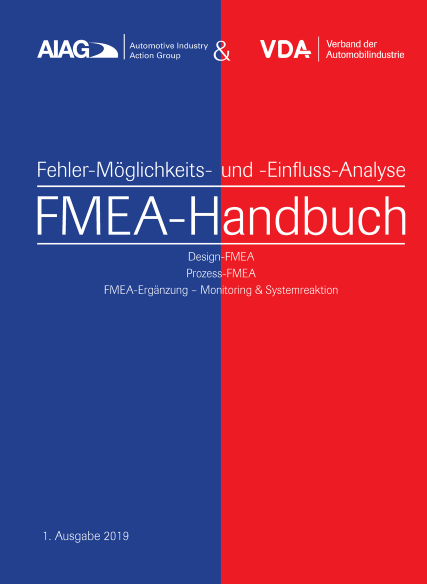
Diese Analysemethode wurde entwickelt, um die Zuverlässigkeit komplexer Entwicklungs- und Entwurfssysteme im Bereich der Weltraumforschung und der Kernenergie zu analysieren.
Es wurde erstmals von der amerikanischen Firma NASA im Apollo-Projekt angewendet. In den 1980er Jahren begann es, in der Automobilindustrie eingesetzt zu werden.
Die FMEA wird verwendet, um:
- Produkt- / Prozessfehler zu untersuchen und zu bewerten
- mögliche / potenzielle Ursachen zu identifizieren
- Wege zu definieren, wie das Risiko durch geeignete Maßnahmen zu identifizieren und zu beseitigen
- Fehlerursachen zu minimieren, bevor der Kunde (intern oder extern) die Folgen von Fehlern spürt
Heute wird FMEA Verwendung von fast allen Automobilherstellern gefördert.
In Zusammenarbeit mit den internationalen Organisationen AIAG & VDA trat 2019 eine neue harmonisierte FMEA in Kraft. Obligatorisch gilt für alle Zulieferer der Automobilindustrie.
Die „ursprünglich alte“ Struktur der FMEA wird außerhalb der Automobilindustrie immer noch akzeptiert. Die Methode kann in anderen Branchen sehr praktisch angewendet werden, um Risiken in Prozessen zu identifizieren und zu reduzieren (z. B. HACCP – „Gefahrenanalyse und kritische Kontrollpunkte“ – „strongHazard Analysis and Critical Control Points“- Gute Herstellungspraxis – da aus einem Lebensmittelstandard eine Variante der FMEA abgeleitet wird).